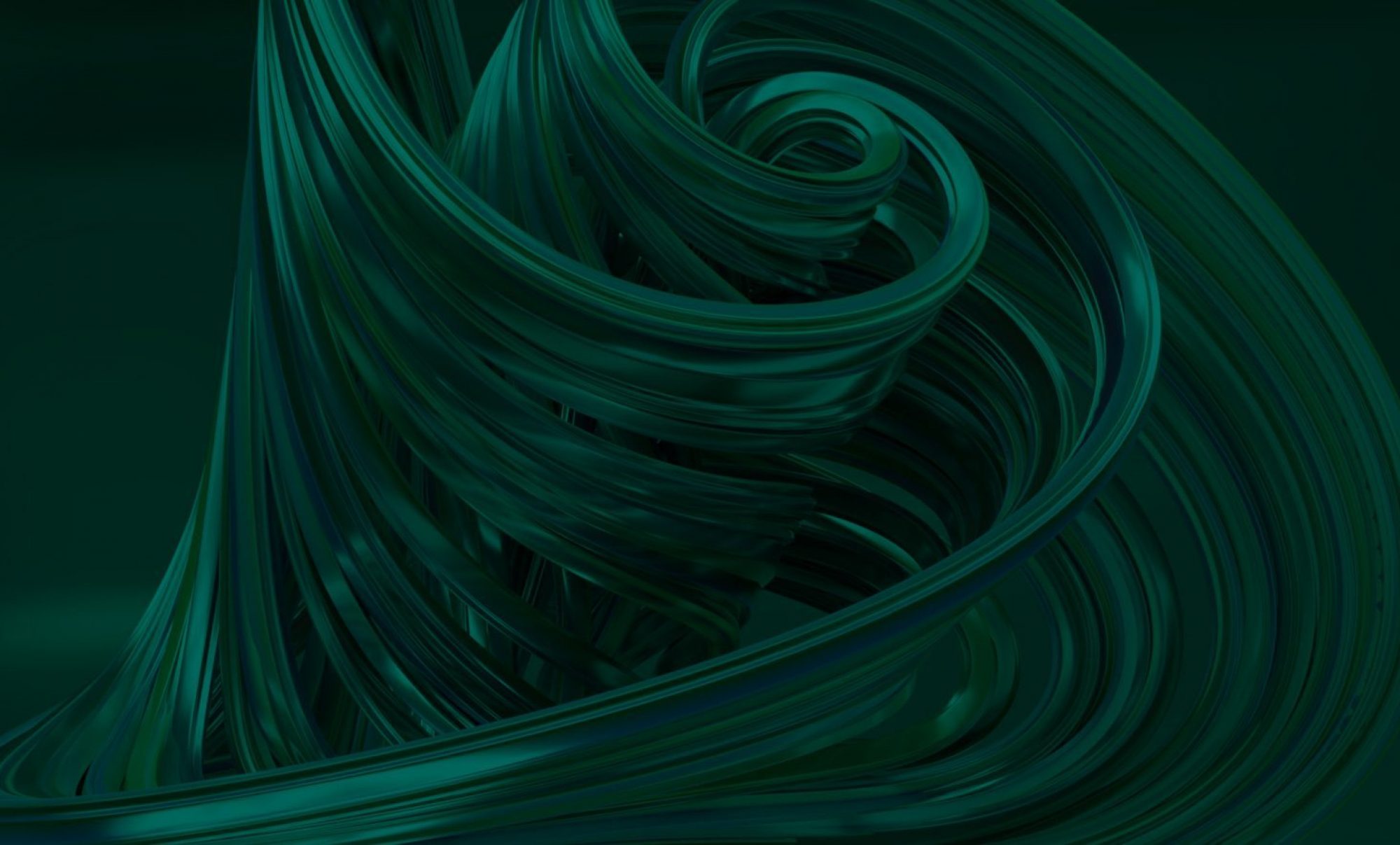
Extending design software for ethylene furnaces
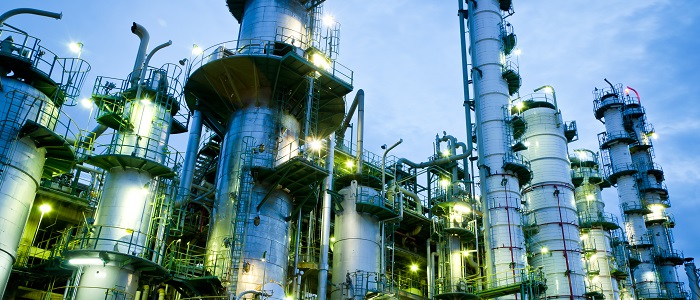
Ethylene is the lego brick of the petrochemical industry: it is the basis of many products like plastics and rubbers. The furnaces that are used to make ethylene are economically important installations. Technips SPYRO® software is one of the top packages for designing them. But SPYRO® can also be used in the process control during operation.
Ethylene can be made for example from naphta, which in turn is made from oil. The naphta is ‘cracked‘ by heating it. This turns the relatively large naphta molecules into smaller ethylene molecules. Obviously, this process has to be done as efficiently as possible.
Finding an optimal design for an ethylene furnace relies heavily on software to simulate the processes in the furnace. This software not only models the temperature distribution and flow in the furnace but also the chemical reactions that take place. Technips SPYRO® software is one of most advanced packages for this simulation. It is known for its accuracy and for the reliability of the process description. Also, it is capable of a good prediction of the emission of poisonous nitrogen oxides (NOx).
Extending with new functionality
For ethylene furnaces, it is important to constantly control the process based on variables like pressure and temperature. This type of control requires accurate prediction of the effects of control operations. Such predictions can be made with a special version of the SPYRO® software which can be coupled directly to the control system: Online SPYRO®. This online version was based on a 15 year old version of the SPYRO® code. With support from VORtech, Technip now updated the online version by integrating the developments that were done on the design version of the software.
The online version clearly has to meet serious requirements. For example, it needs to be extremely stable. In the offline version, the user interface can detect and handle problems. But the online version is called constantly by the control software and a failure of the software would be very problematic. VORtechs employees collaborated with experts from Technip to introduce a number of improvements to make the software more robust.
Performance improvement
Apart from the functional extension, the software had to be made faster. A higher performance could be reached by doing multiple computations simultaneously. In addition, the sensitivity of the variables had to be passed on so that the control software can make the necessary corrections. For this, VORtechs knowledge of numerical analysis proved to be essential.
It is expected that the online version of SPYRO® will prove to be a major improvement for producing ethylene and derived products. We are happy to have contributed.